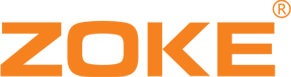
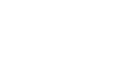
Welding strip is an important raw material in the welding process of PV module, and the quality of welding strip will directly affect the collection efficiency of PV module current, which has a great influence on the power of PV module.
In the process of welding with the series battery must be welded firmly, avoid the phenomenon of false welding. Manufacturers in the choice of welding belt must be based on the choice of the characteristics of the battery plate to determine what the state of welding with. Selection of the general standard is according to battery slice thickness and short-circuit current to determine the welding zone thickness, welding with the width and the battery main delete line width consistent, welding with the degree of hardness is generally determined in cell slice thickness and welding tool. Manual welding requirements of welding with the softer the better, soft state of the welding zone in iron through good and cell contact together, welding stress generated in the process is very small, can reduce the rate of fragmentation. But the soft welding belt tension resistance will be reduced, it is easy to pull off. For automatic welding process, welding strip can be a little hard some, like this is advantageous to the welding machine welding with straight and pressure welding, too soft welding machine welding easily deformed, thereby reducing the finished product rate.
Welding welding belt use electric iron according to the different components have different choices. Generally speaking, welding lamps and lanterns small PV modules of iron low, small component itself smaller, on the iron heat requirements is not high, generally 35W electric soldering iron can meet the welding requirements of lead-free solder, but the welding lead-free solder with recommended by the manufacturer as far as possible the use of 50W electric iron, but also to the use of lead-free long-lived flatiron head, because the lead-free solder oxidation is fast, the damage of the soldering iron head considerable.
Lead welding with welding is relatively easy, as long as the choice of proper flux, solder iron temperature compensation enough can be, but lead-free welding with welding indeed trouble a lot, many manufacturers in this regard a headache. First, lead-free soldering to select a suitable electric iron, for manufacturers, power adjustable lead-free soldering station is a good choice, lead-free soldering station is generally DC power supply and voltage can be adjusted, the advantages of DC electric iron is fast temperature compensation, which is incomparable to the AC temperature adjustment electric soldering iron. Lead-free welding with welding according to battery slice thickness and area should choose 70-100w iron and less than 70W iron general in the lead-free soldering problems arise. Also on the market many kinds of lead-free thermostat AC iron (magnet thermal control) is not suitable for welding a large area of the cell, because solar cell silicon thermal performance is good, the heat of the soldering iron head will rapidly transferred onto silicon wafers, instantly making the temperature of the soldering iron head is reduced to below 300 degrees, iron temperature compensation to ensure the temperature of the iron is increased to 400 degrees, can not guarantee the lead-free soldering of the firm, phenomenon is cells in welding occurred in the process of crackling noise, serious immediately so that cells appear crack. This is because the soldering temperature is low caused by shrinkage stress. Lead-free soldering iron head oxidation is very fast, to maintain cleanliness of the soldering iron head, in a heated state best will embedded solder iron head, before use to get rid of the soldering iron head excess solder. The contact tip and welding with the end to try to repair and weld width is the same with the contact surface should be smooth. Welding flux to use lead-free flux residues.
In lead-free soldering welding with the process, production manufacturers should pay attention to the workers to adjust the welding habits, the mobility of lead-free solder is not good, the welding speed is much slower, welding must wait until solder completely melted to walk again after iron, the iron to walking, if it is found that the solder solidification process of iron, iron head temperature is low, to regulate the temperature of the soldering iron head, elevated to the soldering iron head smooth mobile, solder smooth flowing.
Correct use of lead free solder
With the EU ROHS directive implementation in June 2006, the export of China's photovoltaic industry faced with lead-free, lead-free solder with with traditional tin lead solder zone, there are many drawbacks. How to overcome these disadvantages are numerous photovoltaic manufacturers urgently need to solve the technical problems.
Lead-free soldering strips according to the coated solder composition is divided into many kinds, the lead-free solder is most widely used is 305 solder, which silver containing 3%, copper containing 0.5%, the advantages of the solder is good welding performance, solder Shuo is high, the melting point is 218 DEG C, used in battery sheet welding of welding temperature is very high, ordinary internal heating type electric soldering iron is difficult to meet the temperature requirements, so with lead-free solder welding to use high power electric soldering iron, the general principle of recommendation is welding high 30 - 40W than the lead free soldering, such as original use 35W electric iron, lead-free soldering to use 70W electric soldering iron.
The poor mobility of lead-free solder, welding to and tin coated with solder fully after the melting to iron, go to slow the speed of iron, iron head rush melting solder slow moving, if it is found that the solder solidification or incomplete melting phenomenon that soldering iron head temperature compensation is not enough, soldering iron head temperature is below the solder melting point, on the market a lot of lead-free thermostat electric iron most prone to this phenomenon, when the temperature reaches 400 DEG C electric soldering iron head contact to the cell, the temperature of the soldering iron head will suddenly dropped to 250 DEG C, the welding connection to continue. Manufacturers recommend selection of high iron head of lead-free soldering station, by adjusting the DC voltage to regulate the temperature of the electric iron, do not use hot disk control thermostat electric iron. Requirements for welding pieces of different types of battery electric iron is not the same, generally large thickness of the cell of iron to high |
Back |