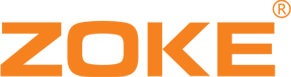
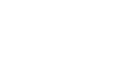
Due to the harm of Pb to human body and environment, the use of Pb in electronic industry will be prohibited in the near future. In order to seek the substitution of eutectic or near eutectic SnPb solder in the electronic packaging industry, a wide range of Pb free solder has been studied extensively. Among them, eutectic SnAg and eutectic SnAgCu solder as potential non Pb solder, has the characteristics of shear strength, creep resistance, good thermal fatigue life and so on.
During the welding process, a layer of intermetallic compound (IMC) is formed at the interface between the molten solder and the substrate. The formation is controlled by the temperature and time of the reflow soldering process, and the thickness increases with the increase of the time during the service. The research shows that the intermetallic compound is a key factor to affect the reliability of solder joints. Thick intermetallic compound layer can lead to the decrease of fracture toughness and low cycle fatigue resistance, which leads to the decrease of solder joint reliability. Because of the different composition of lead-free solder and traditional SnPb solder, the reaction rate and reaction products of Cu, Ni and AgPd are different, so that the reliability of solder joints is different. In this comprehensive and systematic study of Sn96.5Ag3.5, Sn95.5Ag3.8Cu0.7 and Sn95Sb5 lead-free solder and a variety of substrates and devices formed surface mount solder joint reliability, and now some of the research results to do a brief introduction.
Lead free solder and Au/Ni/Cu solder joint reliability of the solder joint reliability experiment selected surface mount components for type 1206 ceramic resistance. The pad structure of FR4 printed circuit board is Cu/Ni-P/Au, among them, the thickness of Ni-P layer is 5mm, the content of P is 12 at%. The solder used for the above lead-free solder and 62Sn36Pb2Ag. The reliability of solder joints during aging process was investigated by using shear strength test method. Fig. 1 SEM photographs of SnAg/Ni-P/Cu solder joints. The SnAg/Ni-P interface is found to have Ni3Sn4 generation, and its thickness increases with the aging time. SnAg solder joint consists of Sn matrix and Ag3Sn particles embedded in them. There is a small amount of chip Ni3Sn4 near the interface. This is due to the dissolution of Ni in the solder during the reflow process and the subsequent cooling process. Compared with the SnPbAg solder joints, the aging of the SnAg solder joint microstructure of the rough to be slightly more, the size of Ag3Sn particles is almost no change with aging time. Fig. 2 the relationship between the shear strength and the aging time of SnPbAg and SnAg solder joints. Obviously, the strength of SnPbAg solder joint decreased with the prolonging of aging time, and its strength decreased by 29% after 1000h aging. The SnAg solder joints in the early aging, its strength than the SnPbAg solder joint high, but 250h aging, the solder joint strength decreased dramatically. At the end of the prescription, its strength is less than 30% of its original strength. Fracture analysis shows that the fracture modes of SnPbAg and SnAg solder joints are obviously different. For snpbag solder joint, before aging, solder joint inside the solder plastic fracture; as time continues, ni3sn4 layer thickness increases, crack in ni3sn4 layer and with Ni-P interface generation and make the shear strength of the solder joint decline. SnAg solder joints at the beginning of the aging process with the same SnPbAg solder joints, but more than 250h, Ni-P layer began to fall off from the Cu matrix, solder joint shear strength decreased significantly. In the process of reflow and aging, the solder and the Ni-P layer will occur between the layers of diffusion, the formation of intermetallic compounds at the interface. The bond strength between Ni-P and Cu matrix is mainly through the Ni-P in the chemical plating process to fill the small pits of the Cu surface and through the interaction between the atoms and the. Below 400 C, the interaction between Ni-P and Cu will not affect the interfacial bonding strength. In this experiment, the Cu/Ni-P layer structure in reflow soldering and aging treatment process under the temperature is less than 300 degrees Celsius, so the heat treatment itself does not have a great impact on the Ni-P/Cu bonding strength. The mutual diffusion elements in the solder and Ni-P are Sn and Ni. The electron probe test shows that the Ni3Sn4 layer on the interface is less than P, that is, P exists only in the remaining Ni-P layer. P is excluded from the inter diffusion layer due to its low solubility in Ni-Sn intermetallic compound, which will lead to the increase of P content in the remaining Ni-P layer. Figure 3 results of the P content of the content in the center of the remaining Ni-P layer in the SnPbAg and SnAg solder joints. Visible, without aging treatment of Ni-P solder joints in the P layer SnAg content is higher, in the aging process and a higher rate of rise, until about 250h after saturation. Obviously, the reaction of SnAg and Ni-P in the process of reflux is faster than that of the Ni-P layer P before aging. And in the subsequent aging process, although snpbag and snag with Ni-P reaction rate is basically the same, but because this snag solder joints in the remaining Ni-P Layer than snpbag solder joint in thin, thickness of Ni-P consumption will still lead to snag solder joints in Ni-P Layer P content is rising at a faster rate. The rapid accumulation of P content of the Ni-P Layer at the same time means that the rapid consumption of Ni, namely, the residual amorphous Ni-P Ni to snag solder side diffusion, will eventually lead to the formation of Cu / Ni-P interface more Kirkendall voids, which decreased the binding strength of Cu / Ni-P. The reaction between SnPbAg and Ni-P was slow, and the effect of the binding strength of Ni-P/Cu was small. SnAgCu and SnSb and snag solder joints is similar, in the aging process are found in Ni-P Layer detached from the Cu phenomenon. Therefore, when the use of high tin lead-free solder should choose thicker Ni-P layer or other kinds of welding disc structure. Solder joint reliability of lead free solder and Cu solder pad is 4 for reflow soldering and scanning electron microscope at the interface near the interface between 1000h and SnAg/Cu before and after 150. There is no aging solder joints by the following components: the SnAg/Cu is located in the Cu6Sn5 interface. |
Back |